Lean Cleaning as a Path to Quality
Cost control and healthy cleaning in K-12 environments.
- By Allen P. Rathey, David Mudarri
- 09/01/16
Lean is about finding the shortest path to quality. Companies
like Toyota helped define what it means when producing
cars. Lean process can help you define and ensure quality cleaning
in your school or district with healthier outcomes at lower cost.
Whether Building Cars or Cleaning –
Take the Five Steps
Whether building cars or cleaning programs, the steps to quality
are the same:
1. Know the Goal – Define Value
2. Break the Job Into Baby Steps
3. Eliminate Steps, Improve Outcomes, Achieve Flow
4. Standardize and Improve
5. Tap Tacit Knowledge or Experience and Share with the Team
Know the Goal – Define Value
Discuss this with your staff and customers, build consensus
and draft a mission statement, such as: “We will produce clean,
healthy, attractive and cost-effective school facilities by first
understanding then addressing school admin, faculty and student
needs, then delivering consistent, high quality cleaning by eliminating
defects and variability in the cleaning process.”
Break the Job Into Baby Steps
This is the key to achieving the goal in step one. You must know
exactly which tools and processes enable reaching the goal. For
example, the steps in a classic floor cleaning process are as follows:
Mop and Bucket Cleaning
1. Sweep floor with dust mop and dispose of soil.
2. Fill a standard mop bucket with water, add chemical.
3. Dip mop in bucket and wring.
4. Mop floor.
5. Rinse and wring mop.
6. Apply mop to floor, continue “cleaning” and redepositing some soil.
7. Rinse and repeat.
8. Rinse out dirty bucket and plan additional cleaning to restore floors.
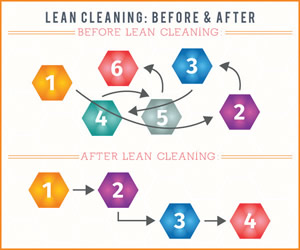
Eliminate Steps, Improve Outcomes, Achieve Flow
To eliminate steps and while improving outcomes, a classic
lean application being used by forward-thinking schools
is to abandon traditional mops and mop buckets in favor of
battery-powered systems that utilize a mop-bucket-sized rolling
platform to dispense cleaning solution onto floors, agitate it then
vacuum it off in one step, insuring consistent concentration of
cleaning solution while eliminating the spreading of dirty water,
some pre-cleaning, and follow-on floor care. Here are the steps in
this new method:
New Lean Method (with battery-powered cleaning platform)
1. Sweep floor with dust mop and dispose of soil (this can be
reduced or eliminated in some cases as the vacuum of the
battery-powered cleaning platform can pick up light soil without
a separate step).
2. Fill cleaning bucket of battery-powered unit, add chemical.
3. Open dispensing spigot to release clean solution onto floor as
you walk, simultaneously agitate by walking across floor with
onboard microfiber scrub pad in “down position”, pick up
soiled solution as you walk with squeegee/vacuum tool engaged
on floor behind cleaning pad.
4. Empty and rinse soiled solution tank.
Since the choice of tool determines the steps involved, select
tools that enable job completion with the fewest steps, then identify
and diagram the value stream to eliminate waste. Simplify
jobs by identifying each and every crucial step and eliminate waste
or backtracking.
The accompanying Lean Cleaning chart illustrates how reducing
steps cuts waste and improves workflow. Apply the principles
to develop cleaning flow charts (examples include dusting, restroom,
floor care and other lean process flowcharts).
Reduce or eliminate stop-start or task-switching interruptions
and apply the new lean processes throughout your operation,
resulting in a significant step and labor reduction.
Standardize and Improve
Standardize best current cleaning practice. The goal of standardizing
is to help ensure cleaning is done the same way every
time for consistency.
It evens-out the workload so each team member works steadily
but not hard (think tortoise not the hare). Standardizing provides
a baseline for improvement.
Continuous improvement is only possible when there is clarity.
Create video (with permission) of field cleaning activities, view the
video as a team, then adopt group improvement suggestions and
build them into the new, better lean cleaning standard.
Tap Tacit Knowledge or Experience
and Share with the Team
Tacit knowledge is gained through experience. Use a buddy
system of training to pair new hires and workers needing coaching
with accomplished team members. Help team associates grow and
realize higher potential.
Remember Your Workers
Lean is about reducing waste, not the workforce. It is a tool for
improving the work through the workers. A Toyota executive said:
“…We had a saying, ‘mono zukuri wa hito zukuri’ which
means ‘making things is about making people.’ If people want to
succeed with lean… they have to emphasize people development
and making leaders capable of delivering improvements.” (from
the book, The Toyota Way, by Liker and Meier)
Lean is about streamlining processes. Workers in lean cleaning
work smarter not harder, and adopt a set of tools, behaviors and
practices to reach higher levels of greenness, healthfulness, quality,
cost-effectiveness, and overall improvement.
This article originally appeared in the issue of .
About the Authors
Allen P. Rathey is an educator specializing in Healthy Facilities. He has assembled an advisory group of dozens of scientists, PhDs, facility and public health experts, who share his passion for helping people everywhere create and maintain safe, healthy, indoor environments. He is past-president of The Housekeeping Channel (HC), The Healthy House Institute (HHI), and The Healthy Facilities Institute (HFI). He is the principal of Winning Environments, LLC, promoting best practices that enhance the living environment. Call him @ 208-724-1508 or email [email protected]. Allen provides advisory and consulting support, in person, by phone, via published articles, social networks, and through seminars and webinars.
David Mudarri, Ph. D., is a retired senior EPA advisor, devoted to advancing public health through indoor air quality education and the development and promulgation of state-of-the-art process and tools. After retiring from EPA, Dr. Mudarri served as the technical editor of ASHRAE's Indoor Air Quality Guide, authored IEHA’s Clean and Healthy Schools For Dummies, and produced papers on the impact of climate change on indoor air quality, building codes and indoor air quality.