AMR Scrubbers Free Up Staff for More Human-Centered Duties
By Catherine Merritt
So you are ready to think about contemplating getting ready to take the leap to maybe investing in autonomous technology? Good for you! Autonomous Mobile Robots (AMR) are the future; Isaac Asimov and the rest of classic sci-fi have been telling us this for decades. Whether sci-fi is predictive or society is derivative is a TED Talk for another day and probably a different publication. But I digress. Moving to autonomous equipment is a big step. My company, SSC Services for Education, provides custodial, grounds, and maintenance services to K–12 and higher education facilities. Five years ago, we chose to leap into the world of AMR scrubbers. And today, we share the lessons learned as we built our robotic fleet and recommendations for success from our internal Product Review Team.
The Basics
Let’s start with the “Why.”
If your move to AMR is driven by a desire to reduce labor and save money, move on. In our tens of thousands of hours of autonomous run time, AMR has never reduced our staffing levels. What does it provide? Efficiencies in detail. Robots are great for taking over labor-intensive but dull and repetitive tasks. AMR allows our associates the time to focus on the human-centric details that make an impact in a facility. It also helps to ensure consistency in floor care, even during this challenging hiring economy.
The “why” is also innovation. Gone are the days when adding a magnet strip to the front of the vacuum to pick up staples was the game changer. The room-mapping technology ensures that no areas are missed and no corners are cut. It’s consistency; once a space is mapped, every nook and cranny will be retraced and cleaned, every time. Depending on the learning program, the AMR will automatically map out the most efficient path. It’s built-in quality assurance. We have a historical log of imaged maps and detailed use hours. It’s job satisfaction. Hour after hour, night after night, month after month on a scrubber isn’t developing people’s skills—it’s racing them towards monotony and burnout. Instead of Floor Techs, develop Robotics Operators on your teams to elevate responsibilities and empower people.
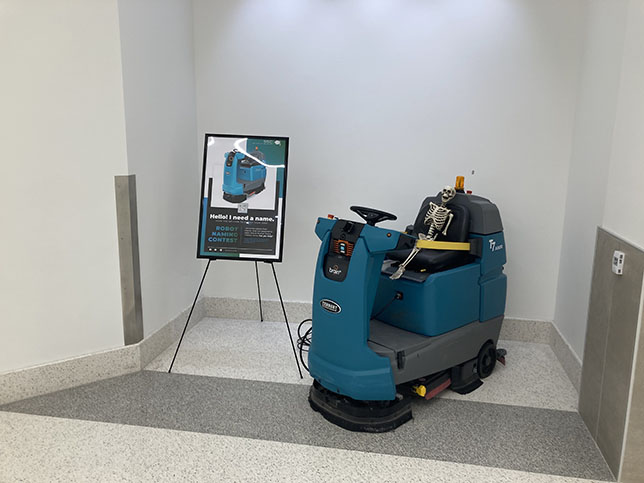
Photos Courtesy of SSC Services for Education
The Equipment
There are two sides to each AMR Scrubber—your familiar scrubber and the autonomous brain. Most AMR units consist of the scrubber manufacturer and a second company that maintains the AI. Start with what you are comfortable with, what already works best in your space. The brands we chose to use were a matter of convenience—we already had strong vendor relationships established, and it made sense to continue forward with the same equipment but with the AI addition.
If you traditionally use pad (single or double), cylinder, or orbital decks—stay with that preference in the move to AMR. Consider tank size and battery life, cleanable square feet per hour, and per charge just like you would with your traditional scrubber. A smaller tank and shorter battery may reduce the upfront cost, but it could reduce the productivity of your space.
Vendor support for setting up the unit in a new location—and new and ongoing operator training—is vital to sustainable program success. If something goes wrong, you want to have a local rep available for prompt support. The equipment is too costly for downtime to be tolerated. Another consideration is the choice of purchasing or leasing the AMR. If you lease the unit, a replacement can often be provided in swift order to avoid downtime.
The AI
If you invest in multiple units, many companies provide access to cloud-synced digital dashboards for reporting and fleet accountability functions. Some are decidedly better than others, so in the demo process, make sure to investigate the dashboard features because these can greatly aid in accountability and KPI tracking of a large fleet, and as technology is always progressing, make sure you are tracking the AI’s latest software release so you can take advantage of updates and improvements to the equipment’s functionality.
We have seen two main AI mapping modes: Teach and Repeat is simply a copycat mode able to repeat a map. This mode is beneficial for areas that change their layout. The second is Area Fill-In mode, where the operator traces the perimeter in manual mode, and then AI calculates the most efficient path for the space’s interior. Once an area is mapped, each subsequent use sees the operator simply bringing the scrubber to the starting point, selecting the map, and watching AI take over. Multiple maps and routes can be stored for each starting point to aid in building occupancy timed cleaning as well.
AMR Scrubbers have 360-degree sensors and cameras to control their movements. This includes movement for cleaning as well as safety. They protect themselves with drop-off sensors to avoid stairs or loading docks, as well as with obstacle detection and avoidance for when a piece of furniture is moved to a new location. The safety systems also protect people by automatically detecting and stopping when a first grader who forgot their library book and, in running back to their classroom, steps into the path of a 1,000-pound robot. For additional safety, the sensors overlap, and there are auto-stop buttons and beeps to alert passersby.
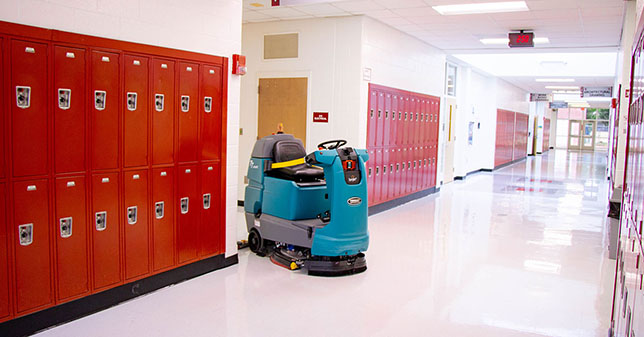
The Facility
Aside from the operator, the building the AMR is placed in is the number-one determination for program success. Not all facilities are created equal, and not all are appropriate for productive AMR use. The most obvious locations are wide-open spaces with few obstacles: gymnasiums; atriums; cafeterias; and wide, long hallways. While some units are designed to be more maneuverable, they still need 7–10 feet to complete a U-turn, so beware of small spaces and older buildings, especially those with small elevators; many are not wide enough or deep enough to allow operators to move the units between floors.
Keep your use goals in mind as you select locations. We advise AMR scrubbers to be allocated to a single building. These machines are delicate, and I have seen more than one succumb to the handling of doorways, thresholds, uneven sidewalks, and lift gates involved in transportation to neighboring facilities. A broken sensor can be a $10,000 repair to a $60,000 piece of equipment; add to that the lead time for such specialized parts, and a unit could be down for over a month. So, for us, it is not worth the efficiencies obtained from increased use by assigning it to multiple buildings because of the increased risk of damage. When we decide to move an AMR to a new location, we have the vendor take on the responsibility of shipping.
The Operators
While the AI is rapidly improving in simplicity and ease of use, not everyone is comfortable with having a robot as their coworker. To get started, hands-on training from site leadership aids in confidence, but when there is knowledge keeper turnover, in-person vendor training produces the best results. We have found that incentives for maximum use in facilities are monthly target-based KPIs with bonuses. Since most floor work is completed when buildings are unoccupied during second and third shifts, this is where the accountability provided by the custom reporting functions aids management, who may work a first shift schedule. The associate responsible for the AMR should have nearby detail-focused tasks to complete while the AI runs the programmed map. Being nearby allows them to check on the unit if it needs assistance and reactivate the program once its needs are met.
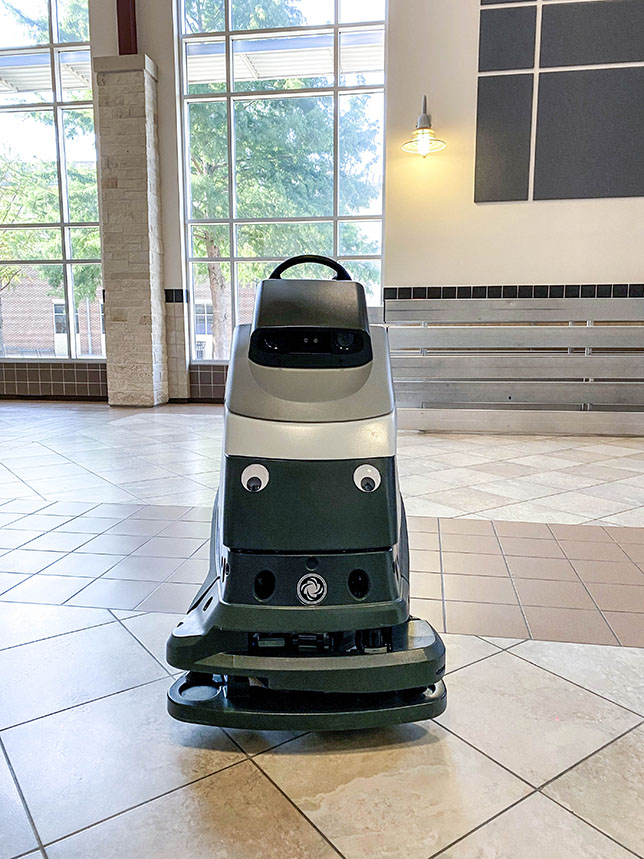
Is Your Program Working?
For SSC Services for Education, the goal is not to reduce headcount or labor hours but to increase building occupant and associate satisfaction. So, our ROI factors into not only usage-based KPIs, which are customized to every location, but building client satisfaction, which can be a harder piece to measure. It is driven by awareness and visibility: Naming contests, incorporation into STEM lessons, and googly eyes. Sometimes it means choosing to run the AMR during occupied times. Where cleaning was previously a disruption, a robot running down the halls is is exciting, curious—and, hopefully, inspiring to a new generation passionate about driving technology forward.
Catherine Merritt is the Director of Communications for SSC Services for Education.