A Rational Approach to Ceiling Product Evaluation
Despite widespread perception that architects and designers are fearless innovators, many, in the author’s opinion, are quite resistant to change. When a product works reasonably well, building professionals tend to stick with it until strong evidence justifies a change.
This article presents a rational investigation comparing acoustic ceiling products made from mineral fiber with thermoformed rigid vinyl types. While manufacturer reputation, economics, availability, and similar factors are important considerations, a rational investigation must look at test data gathered in accordance with industry standards. While performance is not everything, without it, there is nothing.
The basis for the investigation is testing by independent laboratories using recognized industry standards. Committees tasked with developing standards comprise individuals who are active in and knowledgeable about the subject matter. Their work is open to public review and commented on and honed through periodic revision. A document is not issued as a standard until a consensus is reached that it provides a meaningful tool that can be applied throughout an industry.
Some standards used to evaluate ceiling materials arc well-known and frequently cited in product literature and construction specifications. For example, ASTM C423, Standard Test Method for Sound Absorption and Sound Absorption Coefficients by the Reverberation Room Method, and ASTM E84, Standard Test Method for Surface Burning Characteristics of Building Materials. Other standards, including those for strength properties and stain resistance, are less familiar but provide valuable insight for material selection.
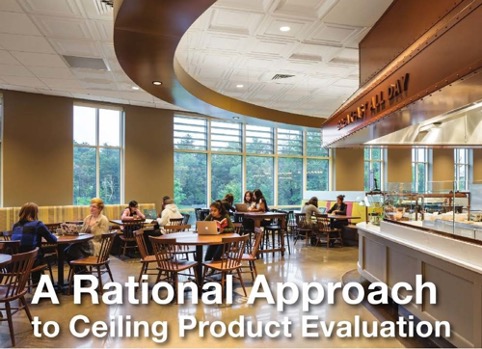
Strength Properties
ASTM C367, Standard Test Methods for Strength Properties of Prefabricated Architectural Acoustical Tile or Lay-in Ceiling Panels, contains procedures to test acoustic ceiling tiles and lay-in ceiling panels for hardness, friability, sag, and traverse strength. Its preface says that some “materials used for absorbing sound generally have a porous, low-density structure. In comparison with many building materials, they are relatively fragile. Materials are available that possess adequate strength and stability and at the same time provide good sound absorption.”
Hardness
This test corresponds with a panel's resistance to impact or indentation, measured by recording the force required to depress a 50-mm (2-in.) diameter penetrator to a depth of 6 mm (1 in.) into the panel. Thermoformed panels are too thin 10 test singly, so multiple layers of the material were stacked to enable assessment. The results are not representative of actual conditions of use, but indicate vinyl is significantly harder than mineral fiber.
Friability
Twelve small squares of the material being tested are placed, along with 24 small wood cubes, in a wood box, then tumbled at prescribed speed for two cycles of 10 minutes duration . The specimens arc weighed after each cycle and the percent of mass lost through abrasion or breakage is calculated. Products losing the most mass are more friable.
ASTM C367 says, "Products that are friable and soft will erode considerably when subjected to rough treatment."
Experience indicates friable products erode considerably even due to ordinary treatment.
Further, "the friability test measures the susceptibility of an acoustical product to edge and corner damage sustained du ring shipping, handling, and installing."
Friability, however, may also relate to release of airborne fibers due to normal building vibrations.
The impact of friability goes beyond the panel appearance and durability. The particles released by mineral fiber products may contain crystalline silica. One major manufacturer' safety data sheet cautions, "Be certain the work site is well ventilated and avoid breathing dust. Exposures to respirable crystalline silica... must be determined by workplace hygiene testing. Prolonged and repeated exposure to airborne free respirable crystalline silica can result in lung disease (i.e. silicosis) and/or lung cancer... " Since particles may also be combustible, the same safety data sheet warns, "Dust deposits should not be allowed to accumulate on surfaces, as these may form an explosive mixture ... "
Sag
After panels are conditioned to a stable ambient temperature and humidity, they are exposed to elevated temperature and humidity, and any of the humidity-induced sag is recorded. The panels are they returned to the initial temperature and humidity, and the recovery sag is recorded. In most cases, the recovery sag represents a permanent deformation. The results of exposure to ambient humidity also suggest how a product responds to moisture exposure via leaks, condensation, and other sources of liquid water.
Transverse strength
Panels are tested in a hydraulic machine, and the load is noted at which the panel breaks or yields and is unable to carry additional loads. The modulus of rupture (flexural strength) is then calculated. A larger modulus indicates greater strength and break resistance.
According to ASTM C367, “Performance characteristics in the handling, shipping, and installing of acoustical tiles or panels are often predicted by strength testing.”
Breakage can also occur during maintenance activities when panels may be moved for above-ceiling access. While new construction employs trained installers, maintenance is frequently performed by untrained tradespersons who are more likely to cause breakage.
Discussion
Thermoformed panel strength properties are at least an order of magnitude superior to the mineral fiber panels in all categories. The results of the tests are summarized in Figure 4.
Stain Resistance
ASTM D1308, Standard Test Method for Effect of Household Chemicals on Clear and Pigmented Organic Finishes, “covers determination of the effect of household chemicals…resulting in any objectionable alteration in the surface, such as discoloration, change in gloss, blistering, softening, swelling, loss of adhesion, or special phenomena.”
While developed to test coatings with household chemicals, the test methodology is frequently applied to diverse types of interior finishes and with chemicals used in industrial, healthcare, and commercial facilities.
Interior finishes often “ugly out” before wearing out. For example, many acoustic ceiling panels are difficult to clean and end up landfilled when they become unsightly. In contrast, stain-resistant and cleanable ceiling panels offer significant advantages in sustainability, economics, and life-cycle performance.
Ceilings are the part of a room in the least physical contact with occupants, yet they are exposed to dirt, grime, and stains from a variety of sources. Air currents from diffusers or ordinary convection carry dust, soot, and aerosols onto ceilings. Everyday substances splash, squirt, or spray upward. Water from leaks, spills, and condensation cause stains and mold on common mineral fiber acoustic ceilings. Panels in suspended ceilings can also get dirty when handled for maintenance access above the ceiling. Despite this, reliable data on ceiling stainability and cleanability has been difficult to find.
Test methodology
Samples were exposed to 14 common staining agents including coffee, red wine, yellow mustard, ketchup, vegetable oil, bleach, povidone iodine, hydrogen peroxide, light machine oil, baking soda solution, vinegar, two types of swimming pool chlorine, and permanent marker. The laboratory compared one of the most widely used white mineral fiber acoustic panels against four colors of thermoformed acoustic panels.
Each staining agent was placed on a specimen panel and allowed to sit overnight. After being cleaned in accordance with the standard, specimens were examined visually, photographed, and the findings are summarized.
Results
The mineral fiber panels showed “significant stains” from all the food products, povidone iodine, calcium hypochlorite, and light machine oil. They had faint stains from bleach and one of the chloride products. The only staining agent they resisted was hydrogen peroxide.
In contrast, thermoformed acoustic ceiling panels proved stain-resistant with either zero or only faint stains from all the agents tested. Permanent marker is the only exception to this observation as it stained all specimens. White showed no staining with any of the 13 other substances. Latte had only “very faint” stains from baking soda, coffee, and bleach—the laboratory noted these “appear as very slight discoloration of the surface where the substance was applied. They are difficult to notice at first glance, and reuire an angled view under lighting to be seen.” Faux metal and wood finishes resisted everything except three harsh chemical solutions: bleach, hydrogen peroxide, and calcium hypochlorite.
Discussion
Mineral fiber panels have porous or fissured surfaces that are vital to their acoustic performance, yet they provide locations through which stains can enter into a panel and become difficult to dislodge. Most mineral fiber panels can be damaged by water or liquid, so there is no effective way to wash them. Further, their edges and corners are fragile and prone to damage when panels are handled or removed for cleaning.
Thermoformed panels are made from rigid vinyl that is impervious to moisture and easily cleaned—factors that make them acceptable for use in hygenic environments such as food handling and healthcare areas. They can be cleaned by brushing, vacuuming, or with water or common household cleaners. They are durable enough to be taken down, cleaned, and replaced without damage.
Other Considerations
Specifiers must balance many considerations when selecting appropriate products for a building, and sometimes strength and stain resistance are not the primary drivers. Some mineral fiber panels, for example, can contribute to the fire-resistance of floor-ceiling assemblies or offer superior noise-reduction properties. Yet, strength and stain resistance impact product durability, the service life, and building sustainability and resilience, and should be considered as part of a holistic approach to design.
When interpreting the test results based on standards, ASTM cautions, “Not all of the tests described in these test methods are necessary to evaluate any particular product for a specific use. In each instance, it is necessary to determine which properties are required. Properties determined by these test methods reflect the performance of the materials under the specific conditions of the test, and do not necessarily indicate performance under conditions other than those described herein. This standard does not purport to address all of the safety concerns, if any, associated with its use. It is the responsibility of the user of this standard to establish appropriate safety and health practices and determine the applicability of regulatory limitations prior to use.
Michael Chusid, RA, FCSI, is a frequent contributor to “The Construction Specifier,” and a consultant to building product manufacturers. He can be reached at www.chusid.com.