Design/Build Value Comparison on Campus
The recent addition of three laboratory buildings on the campus of Colorado State University, completed through three different delivery methods, allowed the university to determine the delivery method that was more cost efficient, efficient, and enjoyable, while retaining a high level of design and construction.
- By Jennifer Cordes
- 12/10/18
Higher education institutions are increasingly challenged today with limited capital construction funding, aging facilities and increasing enrollments.
Colorado State University (CSU) in Fort Collins has grown significantly over the last decade, and in doing so has tested a variety of different project procurement methods to maximize value for their campus. The team of Hord Coplan Macht Architects (HCM) and Haselden Construction had the unique opportunity to work with CSU on three new laboratory buildings, with each building procured using a different delivery method. The team saw this as an opportunity to compare the benefits of each method holding the architect, general contractor, and owner constant.
The team was selected to design and build three separate laboratory buildings over the past 10 years using three different delivery methods: GMP Lump Sum Construction Manager/General Contractor (CM/GC), Design/Bid/Build (D/B/B), and as a unified team for a Design/Build Lump Sum (D/B). This situation provided a perfect opportunity to isolate the team from the equation and test the delivery methods themselves on the following three campus construction projects.
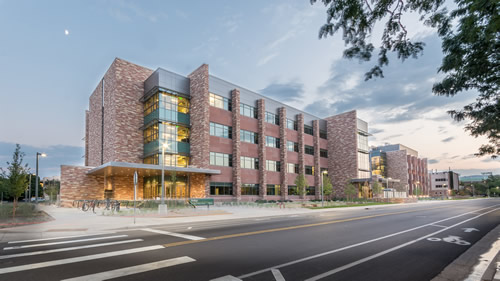
Project No. 1: Suzanne & Walter Scott Jr. Bioengineering Building (CM/GC Delivery Method)
CSU, HCM and Haselden Construction (Haselden) designed and built the 122,000-square-foot Suzanne and Walter Scott Jr. Bioengineering building. The project was procured using the CM/GC method, where HCM was hired through a qualification-based selection process with Haselden brought on as the CM/GC. Our firms contracted separately with the university and the project successfully opened on time and obtained LEED Gold certification.
Project No. 2: Chemistry Research Building (D/B/B Delivery Method)
CSU made the decision to use the traditional Design/Bid/Build (D/B/B) delivery method for the Chemistry Research building, as the capital construction funding was largely provided by the state and available in three phases. Phase one funding aligned with the building design expenditure, phase two with the building core and shell, and phase three with the interior finishes. Instead of waiting three years in an escalating market to begin the project under a Design/Build Lump Sum approach, CSU determined it would be best to leverage the resources with a traditional D/B/B development strategy. On this particular job, HCM was hired through a qualification-based selection process and Haselden won the competitive bid for construction. Once again, our firms contracted separately with the university and the 60,000-square-foot Chemistry building successfully opened on-time with LEED Platinum certification.
Project No. 3: Biology Building (D/B Delivery Method)
The 154,000-square-foot CSU Biology building was cash-funded by the university. The project leveraged a project-specific student facility fee with donor funds to accommodate the debt service on the bond. Again, in an escalating market and since the funding was available all at once, CSU determined that a Design/Build Lump Sum acquisition strategy would offer the best speed-to-market and most expeditious construction schedule.
CSU created robust bridging documents for the Biology building using an in-house team and design criteria consultant. The bridging documents were developed by the team through the procurement to the extent required for the design/builder to provide a lump sum cost proposal. Points were awarded during the interview for “innovative departures” and “structured alternates” that added value to the project and the HCM/Haselden team won the commission by working as an integrated unit finding over $1.5 million in cost savings by introducing a slightly larger four-story building. In tandem with the Chemistry building, the Biology building opened on time with LEED Gold certification. The Biology and Chemistry buildings were planned and designed at the same time and situated side-by-side on the site.
Given the unique situation with the three distinct delivery methods, we collaborated with CSU and Haselden to collect statistical, empirical, and qualitative data to compare the various delivery methods. Our team tracked the speed of the projects by comparing schedules and productivity, quality of the projects through punch list items and cost of the projects through number of RFI’s, added value, change orders, and contingency usage. It was also important to our team to understand the qualitative issues associated with the delivery methods and how the methods affected the team. Interviews were conducted at the conclusion of the projects to gather information from team members regarding each project delivery system.
Findings
Speed: Schedule—We found that the Design/Build Lum Sum (D/B) project design time was 11.5 percent faster than Design/Bid/Build (D/B/B) and 6 percent faster than GMP Lump Sum Construction Manager/General Contractor (CM/GC), allowing our team to start construction more quickly. This was due in part to the extensive work the university did with user groups before the project was awarded to our team for design. CSU Project Manager & Interim Supervisor of Capital Construction Tracey Abel logged hundreds of hours over a six-month period to build consensus toward a common vision amongst various user group.
“We had eight months of time before funding would be available. By spending the upfront time to collect information from each user group, it generated efficiencies and adjacencies that informed the floor plates. By getting through departmental discussions and have consensus prior to sending out the bridging documents, it allowed the Design/Build team to focus on design and not bringing the Design/Build team into long departmental discussions or issues,” says Abel.
Speed: Productivity—The D/B model was 27 percent more productive as compared to the D/B/B model. We attributed the increased productivity to the inclusive process Haselden incorporated with their trade partners. Key trades were involved with creating the D/B schedule and thus understood the manpower needs to meet the schedule. In D/B/B process, the schedule is typically mandated to the general contractor and thus they rarely have time to coordinate an integrated schedule because the trades are selected based on the lowest price and not on their ability to collaborate within a team. This often results in manpower issues on site and lower productivity. Haselden observed that when there is lower productivity on site, profit margins are reduced, and tensions can elevate creating a stressful work environment, increased errors and lower quality craftsmanship.
Cost—The D/B method resulted in an 86 percengt reduction in change orders when compared to the traditional D/B/B method. The CM/GC method resulted in a 61 percent reduction.
We found that the CM/GC process shifted some of the “actual cost” risk onto the general contractor on the Bioengineering building, but we lost the opportunity to spend project savings of $47,000 due to this shared risk. Under the CM/GC delivery method, CSU spent $778,101 of the owner’s held contingency on field changes and value-added (owner-requested) changes in addition to $908,495 of the contractor held contingency, which Haselden was required to carry per the State of Colorado CM/GC contract. As previously noted, $47,000 in project savings remained, which Haselden returned to CSU after substantial completion. Although the return of funds was likely the best alternative, we all recognized that this savings symbolized value that was not included in the project. During the Biology building construction process, Haselden was required to resolve all unforeseen issues ($680,861 worth) within the budget identified during procurement. This allowed CSU to spend their owner held contingency on added scope, such as building out the originally shelled fourth floor and adding state-of-the-art exhibits throughout the first floor to enhance the user experience in the building, including adding a “Living Green Wall,” 10,000-gallon fresh and salt water aquarium, and museum-grade exhibits of the natural history collection.
The most fascinating finding was that in 2009, CSU built the 122,000-square-foot Bioengineering building for $57.4 million. (Note: 2009 was in the middle of the national recession.) Six years later, as the recession was recovering, CSU built the 154,000-gross-square-foot Biology building for $56.7 million. This included the addition of 45 owner changes, which resulted in higher value for the university and the Biology department.
Quality—The D/B project had 92 percent fewer punch list items compared to the D/B/B delivery method and 32 percent fewer than the CM/GC method. We believe this showcased the subcontractors’ involvement and dedication, as well as the overall level of quality with an integrated team.
While it is impossible to agree on a statistic proving “great design,” we can agree that happy and healthy building users are a strong indication of success. Over the last 15 years, CSU has worked hard to improve the CSU student experience and building design is important to the university architect and campus leadership. All three laboratory buildings on campus were developed and approved with input from the CSU Design Review Committee.
“I’m proud not just of the quality of the space, but also of the economy we worked to meet in creating it. It is a high-quality product that represents the students’ dollars,” says Dr. Joe Von Fisher, Ph.D., Colorado State University. “The process, of course, was amazing. We appreciated having HCM and Haselden as partners in this. It was productive. It was fun. And, I count you all as friends now—I know not every project ends that way!”
People—As part of the evaluation process, it was important for the university to understand how the various delivery methods affected those working with and for the university. Finding empirical data to prove the effects on people was challenging, but our team gleaned information from interviews and observations on the job site.
From our observations, it was evident that the D/B and CM/GC projects had a more positive affect on the team members than the D/B/B project. Although Haselden worked hard to maintain a consistent culture on all three job sites, the D/B/B project proved to be the most challenging. Due to the varied productivity and difficult schedule, there was significant personnel turnover and the increased stress on the site of the Chemistry building could be “felt” during subcontractor appreciation events. CSU and Haselden hosted two events on the same day approximately an hour apart. During the D/B lunch there was palatable camaraderie with team members laughing and talking, unlike the D/B/B event where it was nearly silent. In addition, during the family night event hosted by CSU, which allowed the team members’ families to view the building before it was open to the public, no subcontractors from the Chemistry building attended with their families and the only attendees were from the Biology building project teams. Although not scientific proof, these observations point to the notion that an integrated team produces a better working environment.
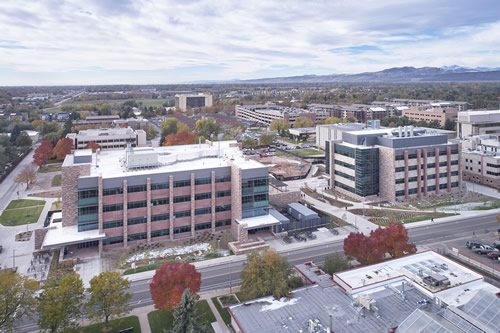
Conclusion
CSU has found that leveraging the strengths of each delivery method allowed them to maximize the funds available for their design and construction projects and, while initially unintended, allowed us to examine the value of the various delivery methods. But it is the D/B delivery method that has brought the most value to the school based on the combination of speed, quality, cost and team satisfaction.
CSU has utilized a design competition model to solicit talented and motivated teams for their projects. With reduced cost, increased speed and design consistency, the university has completed seven D/B projects with six more projects planned. They have evolved their procurement process so that it only takes six months to develop performance criteria for new projects. They have also continued to update campus standards and technical specifications to advance the process and allow for innovation from the industry.
While there is no doubt that there is a time and place for each delivery method, our data supports that, if the client has a trust-based culture and sets clear expectations, the Design/Build Lump Sum process is more cost efficient, efficient, and enjoyable, while retaining a high level of design and construction.