Too Hot, Too Cold, Too Expensive: Energy & HVAC
- By David Mount, Shane Day
- 11/01/14
PHOTOS BY BEN BENSCHNEIDER, COURTESY OF MAHLUM ARCHITECTS.
When contemplating the myriad HVAC options for a new school facility, school districts often weigh construction costs, energy efficiency and long-term maintenance to select the best option. Current codes, industry standards and best practices ensure a baseline quality of occupant comfort and health provided by the mechanical system. While there are standards around human comfort, this ideal is extremely subjective and elusive to many school district facility managers. Addressing concerns around comfort is a strong motivator to not deviate from systems familiar to maintenance staff. Regardless of if these systems are energy-efficient, operationally cost-effective, or really provide comfortable and healthy indoor environments, familiarity allows operators to manipulate and adjust to help address occupant complaints.
However, research shows that comfort can have a significant impact on occupant performance, especially for student learning. What happens when student and staff comfort is a primary goal of a school district? How does the design team ensure an HVAC system that delivers comfort and still meets important cost and maintenance parameters? For Bainbridge Island School District, which serves a small, rural island community 30 minutes by ferry from downtown Seattle, comfort drove HVAC decisions with compelling results.
PHOTOS BY BEN BENSCHNEIDER, COURTESY OF MAHLUM ARCHITECTS.
ENSURING LONG TERM VALUE FOR A SAVVY SCHOOL DISTRICT
The community of Bainbridge Island puts a priority on education and has one of the highest performing school districts in the state of Washington. Families move to the island for its schools, as well as its preservation of the natural environment. When the voters approved a bond in 2006 to replace one of the island’s three elementary schools, the district sought to create a state-of-the-art preK-4 facility that would reflect the community’s focus on its students and connections to the environment. At the same time, the district had to meet the demands of the fiscally responsible population to realize a high value return on their investment. They needed to spend construction dollars wisely by building a new Wilkes Elementary School that was comfortable, durable, long-lasting and have low operational costs.
“We wanted Wilkes Elementary School to be an effective model of fiscal responsibility that contributes consistently to student and staff comfort,” says Tamela VanWinkle, director of Facilities and Capital Projects for Bainbridge Island School District.
PHOTOS BY BEN BENSCHNEIDER, COURTESY OF MAHLUM ARCHITECTS.
HARNESSING INFORMATION FROM THE EXISTING SCHOOL
To help understand how the design could best balance these competing concerns, Bainbridge Island School District and design team members from Mahlum Architects and Arup brought community stakeholders together to prioritize strategies for building systems. They sought a solution for the school’s mechanical systems that could be efficient while addressing their primary concern — human comfort, which was distinctly lacking in the existing school.
Four separate, single-story buildings comprised the existing school, which was built in the 1960s and had undergone several renovations. Aging systems, tattered interior materials, and ongoing drainage issues resulted in poor indoor air quality. Small windows permitted little daylight and isolated students and staff from their natural surroundings.
To set a baseline for discussion about building systems for the new school, the design team analyzed energy use and energy costs of the existing system that was fed by the island’s electric service utility and on site propane tanks. The team found that a modern facility built to minimum Washington energy code standards would save $25,000 in annual energy costs, but an even more energy efficient system implementing heat pumps would save an additional $25,000-30,000 annually.
This analysis, as well as the possibility of significant long-term savings, suggested that a decoupled mixedmode system – one that mechanically delivered fresh air directly into rooms, while allowing for natural ventilation, and also provided mechanical conditioning through radiant flooring — would best provide optimal indoor comfort and address the school district’s requirements. As the team undertook extensive studies to verify this strategy, occupant feedback was integral to the design and would guide operations.
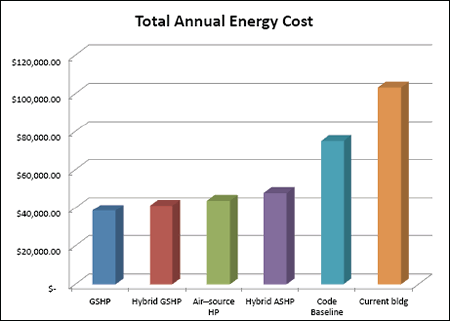
ENVIRONMENT’S IMPACTS ON LEARNING
To further support their plan for a decoupled mixedmode system, the team integrated the data from the original school with industry research about the impacts of indoor environmental quality on learning. Research studies by the Center for the Built Environment, the Environmental Protection Agency and the Heschong Mahone Group have shown natural daylighting improves test scores, while fresh air helps keep students healthy and alert. Good acoustics improve absorption of instruction, and comfortable temperatures boost student productivity. The district was intent on ensuring that these parameters would be oriented to benefit their students, even if the building systems were unfamiliar to maintenance staff.
Crucially, maintenance staff was on board from the beginning. They participated in the district’s advisory group and were involved in design and construction decisions about building systems, providing review of HVAC systems. Often overlooked in organizations, the maintenance team brought practical and historical experience to the design team.
“Maintenance and operation staff involvement was highly encouraged from project inception. Our early participation in evaluating unfamiliar systems helped the district understand the benefits of the mechanical design and provided opportunities for us to find efficiencies within the systems.” says Bernie Mejia, Maintenance Lead for Bainbridge Island School District.
CONCRETE GOALS FOR THE HVAC SYSTEM
The results of the team’s discussions with faculty, staff and parents uncovered several specific requirements: including operable windows must be available in all rooms, and, since the majority of the occupants are under 4-feet-tall and often work and sit on the floor, heating near the ground plane was paramount.
The team’s analysis of the existing school revealed further necessities to optimize indoor air quality: the air ventilation system would use 100 percent outside air to avoid recirculation of indoor air, and carpets would be eliminated to address concerns about dust, cleanliness, and long term maintenance.
Finally, since the 2008 recession had caused reductions in state and local funding to the district, it was essential that the system be energy efficient and minimize operational costs. Every dollar saved in the facility operations would allow more funding for teaching and learning.
OVERALL SYSTEM SOLUTION
Heating at Wilkes is provided by a hybrid groundsource heat pump system, including 45 bores each 300-feet deep, supplemented by a 200-kW electric boiler. A ground-source system without a boiler would require nearly twice as many bores to provide heating for peak use. Peak use at Wilkes is just 10 percent of the time, so the supplemental boiler is much more cost-effective. Since the climate of the Puget Sound in Western Washington is mild, no mechanical cooling is required.
Despite a higher capital cost than a traditional boiler or hot air furnace, a heat pump system was studied because of its high coefficient of performance (COP). Because heat pumps are heat transfer devices, the only energy they use is electrical energy in the compressors. A typical heat pump produces three times more much energy than it uses in electricity (i.e. a COP of 3.0), so the COP greatly reduces the annual operating cost. Four heat pump alternatives were considered to heat hot water — an air-source heat pump, a ground-source heat pump, and hybrid alternates for each of these with peak heating supplemented by electric boilers. A hybrid groundsource heat pump was ultimately selected for its life cycle cost savings versus code baseline, as well as qualitative considerations such as reduced noise, plant space and robustness of the equipment.
To deliver heat and ventilation to the occupied spaces in a manner that ensured student comfort, the design included radiant floors, demand control ventilation, dedicated outdoor air units with air-side heat recovery and the ability to provide natural ventilation through operable windows.
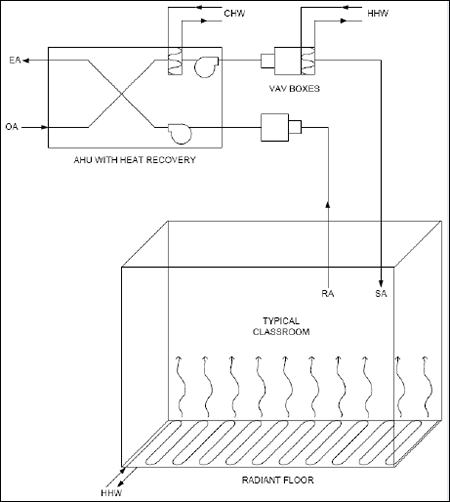
To further ensure fresh air throughout the school, the team relied on operable windows during mild weather coupled with a mechanical ventilation system via dedicated outdoor air units during the colder weather. The outdoor air units, in conjunction with variable air volume (VAV) boxes control ventilation airflow rates to each space and preheat the air to the same temperature as the classroom. The radiant floor is sized to provide enough heat to overcome losses through the envelope. Triple glazing in classrooms helps to prevent heat loss.
The radiant floor system delivers heat directly at
occupant feet and produces much less noise than other options. However, the thermal mass of a radiant floor system hinders quick reaction of a system to changes in use. Since slab thickness determines response times, the design at Wilkes implemented a 2-1/2-inch topping slab over a layer of insulation separating it from the structural slab below. Although this increased the cost compared with imbedding the radiant tubes in the structural slab, response times are greatly improved. The school’s maintenance staff has been thoroughly trained in programming the radiant floor for optimal use during the school day and across the calendar year.
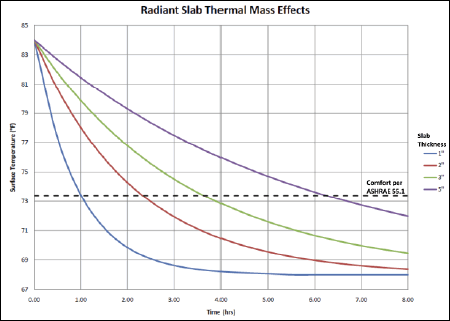
The team also analyzed the potential thermal comfort issues associated with the school’s large expanses of glazing. Even when the space temperature is satisfied, occupants can feel uncomfortable due to drafts and mean radiant temperature differences caused by glazing surface temperatures. Using Arup’s comfort analysis software, the team evaluated a typical classroom, the library, and the commons for potential issues, finding that only the commons required additional shading to avoid uncomfortable conditions in September, the warmest month when school is in session. The following diagram indicates the worstcase scenario in the commons and was used to inform the architect’s glazing design in this area.

MEASURABLE RESULTS
After two years of operations, there have been many reports that the system is providing a high level of comfort to the students, faculty, and staff, especially the radiant floor. The continual involvement of district maintenance staff during the design and construction period virtually eliminated the typical “break-in” period of building systems as personnel take over and fine tune operations of a facility. Facilities staff have implemented a few tweaks — such as revising the door hold and closure hardware to increase easy access to outdoor play areas and monitoring the ground loop water temperature to determine the best temperature for stable operation of the electric boiler. “The early investment of time and learning by the maintenance staff translated into a seamless initial occupation and transfer of building ownership and operation from the contractor to the school District.” says Bernie Mejia, Maintenance Lead for Bainbridge Island School District.
Overall, the new Wilkes Elementary School is an innovative place for learning that reflects community values and is physically and visually knitted to the natural environment. Fresh air, daylight, and views suffuse all educational spaces, while natural wood finishes with unpolished rubber and honed concrete floors add warmth, durability, and ensure high indoor air quality. It is truly a comfortable place for students to learn.
This article originally appeared in the issue of .